GRP (Glass Reinforced Termosetting Pipe) Pipes and Fittings
GRP Pipes are specially manufactured for use in many type of projects, especially National Water Society, dams and HEPP projects. GRP pipes are produced at standard rigidity values for standard projects, as well as for special projects, they are produced at special rigidity values that go beyond the standard.
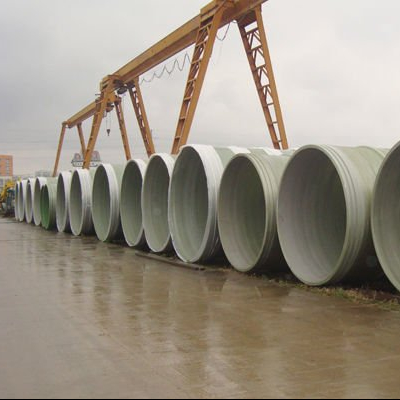
GRP Pipe General Features
The range of stifness is in standard SN500, SN1000, SN2500, SN5000, SN10000/m2 can be produced and special classes for special projects is possible as per the project necessaries. GRP pipes are produced in pressure class from 1 bar to 40 bar. You can contact us for special pressure range and SN class.
GRP pipes to be used in transmission and network line constructions are produced by AWWA M 45, AWWA C 950, ASTM D 3517, ASTM D 416, ASTM D 3839, ISO 10639, and TS EN 1796 standards.
GRP Pipes are produced from 100 mm to 3000 mm diameter in accordance with international standards. The stiffness value of GRP Pipes is resistant to carrying the peak load, which determines the resistance of the pipe against dynamic loads such as natural soil and backfill material, static, traffic, and negative pressures (vacuum).
Frequency (Rigidity) class SN 500 1000 2000 2500 It is 4000 5000 8000 10000. The connection methods of GRP pipes are divided into bonding and mechanical. Mechanical connection methods are made with gasket, sleeve, and flange.
GRP Pipes are produced in 3, 5, 6, 10, 12, or 18 meters. GRP pipes are produced according to inner and outer diameter series. GRP pipes are resistant to axial tensile forces depending on the design criteria. GRP Pipes are produced according to the fiber winding method or centrifugal casting method.
GRP pipes are also known as FRP pipes. GRP pipes are manufactured using composite raw material technology using fiberglass, polyester resin and silica sand. Glass fiber reinforced plastics (GRP) is a composite material made of a polymer reinforced with fibers.
GRP pipes are designed for weathering, corrosion resistance and durability. In this regard, GRP Pipes / FRP Pipes are the kind of pipes that provide more economical and high performance compared to other conventional pipes.
Areas of use of GRP Pipes, FRP Pipes
GRP Pipes used in pressurized and clean water pipelines,
GRP Pipes uses in main transport and lateral lines for irrigation channels,
GRP Pipes / FRP Pipes used in wastewater and sewage lines,
GRP Pipes used in stormwater drainage and other drainage lines,
GRP Pipes preffered in dam Projects because of high pressure and voluminous water.
GRP Pipes used in Hepp Projects in worlwide,
GRP Pipes used in submarine projects,
Advantages of GRP Pipes
Underground applications, above-ground applications, underwater applications, pipe relining GRP pipes are applied underground and above ground, underwater and reeling method.
GRP pipes have high corrosion resistance. GRP pipes are lighter than concrete, ductile, and steel pipes. GRP pipes can be brought to the desired dimensions by cutting and turning, even in the construction site environment.
GRP pipes are resistant to extreme pressures. GRP pipes have become a preferred brand in earthquake zones due to their flexibility. GRP pipes do not require a cathodic protection line. Thanks to this feature, they have low operating and maintenance costs.
GRP pipes are designed to be compatible with ground movements. GRP pipes are 100% environmentally friendly. significantly reduces the use of elbows due to the angular deviation tolerance in the joints of GRP pipes.
GRP pipes are not affected by ground current. GRP pipes are an insulating material. Thanks to the high resistance of GRP pipes against abrasive substances, there is no increase in friction losses in the pipes over time. GRP pipes save energy in pumping lines.
Handling and Storage of GRP Pipe
During the loading and unloading of GRP pipes, appropriate cloth slings should be used according to the weight of the pipes.During lowering, the pipe should be lowered under control by tying a control rope to one end of the pipe.
Chain or steel rope shall not be used during loading and unloading. If used, one of the ends should not be held by hand for safety and a lasso should be thrown here.
While the GRP Pipes are stacked, planks are used to cut off the contact between the ground and the pipe, and fastening is done with skewer ropes.
While the pipes are being stocked, they are stacked according to the diameters so that the pipes are not damaged.
While stacking, 3 pieces of timber are placed at equal distances between 2 pipes, and the weight applied to the bottom pipe is distributed.
The transportation of GRP Pipes is carried out within the framework of the principles of stacking.
GRP Pipe Storage area is specially preserved.
Since GRP pipes are specially designed against UV light, they can be stored in the open field.
Maximum stacking deflection of GRP pipes: For SN2500 pipes: 2.5% For SN5000 pipes: 2.0% For SN10000 pipes: 1.5%.
GRP Pipes Production Standard & Quality Control
GRP pipes are made of unsaturated polyester resin (UP) based glass-fiber reinforced thermoset plastic designed to be used in the transfer of pressurized and non-pressurized water (drinking and using)
1- GRP Pipe Diameter: The inner diameter or outer diameter declared according to the nominal diameter (DN) class allowed by the standard should not be more than the tolerance value specified in the standard.
Series A (Internal Diameter Defined)
Rated Outer Diameter(DN) |
Pipe Inside Diameter |
Inner Diameter Deviation |
---|---|---|
100 |
97-103 |
±1,5 |
110 |
107-113 |
±1,5 |
125 |
122-128 |
±1,5 |
150 |
147-153 |
±1,5 |
200 |
196-204 |
±1,5 |
225 |
221-229 |
±1,5 |
250 |
246-255 |
±1,5 |
300 |
296-306 |
±1,8 |
350 |
346-357 |
±2,1 |
400 |
396-408 |
±2,4 |
450 |
446-459 |
±2,7 |
500 |
496-510 |
±3,0 |
600 |
595-612 |
±3,6 |
700 |
695-714 |
±4,2 |
800 |
795-816 |
±4,2 |
900 |
895-918 |
±4,2 |
1000 |
995-1020 |
±5,0 |
1200 |
1195-1220 |
±5,0 |
1400 |
1395-1420 |
±5,0 |
1600 |
1595-1620 |
±5,0 |
1800 |
1795-1820 |
±5,0 |
2000 |
1995-2020 |
±5,0 |
2200 |
2195-2220 |
±5,0 |
2400 |
2395-2420 |
±6,0 |
2600 |
2595-2620 |
±6,0 |
2800 |
2795-2820 |
±6,0 |
3000 |
2995-3020 |
±6,0 |
Please contact us for other diameters specific to your project.
2- Thickness: The minimum total wall thickness, including the lining, must be declared by the manufacturer and it should not be less than 3 mm.
3- Rated Length: It must be 3, 5, 6, 10, 12, or 18 meters. Pipes of other lengths are also available upon agreement between the manufacturer and the customer.
4- Tensile Strength EN 1393: Minimum initial specific longitudinal tensile strength per mm of the pipe circumference It is expressed as N.
For pipes that do not need to withstand the longitudinal load created by the internal pressure acting on the pipe at the relevant end loading conditions, the initial specific longitudinal tensile strength of the test pieces taken is σ1 when tested following Method A or Method B using appropriate test pieces for each pipe.
The average value of, in N/mm, should not be less than the values given in the standard according to the nominal diameter (DN) of the pipe under test.
For each pipe, the mean value for the elongation at the break of the test pieces taken shall not be less than 0.25%.
Nominal Diameter | PN 4 | PN6 | PN10 | PN 12,5 | PN 16 | PN 25 | PN 32 |
---|---|---|---|---|---|---|---|
100 |
70 |
75 |
80 |
85 |
90 |
110 |
125 |
125 |
75 |
80 |
90 |
95 |
100 |
120 |
135 |
150 |
80 |
85 |
100 |
105 |
110 |
130 |
145 |
200 |
85 |
95 |
110 |
115 |
120 |
140 |
155 |
250 |
90 |
105 |
125 |
130 |
135 |
165 |
190 |
300 |
95 |
115 |
140 |
145 |
150 |
190 |
220 |
400 |
105 |
130 |
160 |
165 |
185 |
240 |
285 |
500 |
115 |
150 |
190 |
200 |
220 |
290 |
345 |
600 |
125 |
165 |
220 |
235 |
255 |
345 |
415 |
700 |
135 |
180 |
250 |
265 |
290 |
395 |
475 |
800 |
150 |
200 |
280 |
300 |
325 |
450 |
545 |
900 |
165 |
215 |
310 |
330 |
355 |
505 |
620 |
1000 |
185 |
230 |
340 |
360 |
390 |
555 |
685 |
1200 |
205 |
260 |
380 |
415 |
460 |
− |
− |
1400 |
225 |
290 |
420 |
465 |
530 |
− |
− |
1600 |
250 |
320 |
460 |
520 |
600 |
− |
− |
1800 |
275 |
350 |
500 |
570 |
670 |
− |
− |
2000 |
300 |
380 |
540 |
625 |
740 |
− |
− |
2200 |
325 |
410 |
580 |
675 |
810 |
− |
− |
2400 |
350 |
440 |
620 |
730 |
880 |
− |
− |
2600 |
375 |
470 |
660 |
− |
− |
− |
− |
2800 |
400 |
505 |
705 |
− |
− |
− |
− |
3000 |
430 |
540 |
760 |
− |
− |
− |
− |
DETERMINATION OF INITIAL SPECIFIC CIRCLE RIGIDITY (TS EN 1228 ISO 7685) Plastics piping systems for water supply with or without pressure – Glass-reinforced thermosetting plastics (GRP) based on unsaturated polyester resin (UP).
EXAMINATION OF INITIAL RING STRENGTH (TS EN 1226 ISO 10466) Plastics piping systems for drainage and sewerage with or without pressure – Glass-reinforced thermosetting plastics (GRP) based on unsaturated polyester resin (UP) – Specifications for pipes, fittings and joints.
INITIAL VISIBLE STRIP TENSILE STRENGTH EXAMINATION (TS EN 1393 ISO 8521) Plastics piping systems for pressure and non-pressure water supply — Glass-reinforced thermosetting plastics (GRP) systems based on unsaturated polyester (UP) resin
Reviews
There are no reviews yet.