High-Density Polyethylene (HDPE) pipes have revolutionized the piping industry with their durability, flexibility, and resistance to corrosion. In this blog post, we will explore the benefits, applications, and installation of HDPE pipes.
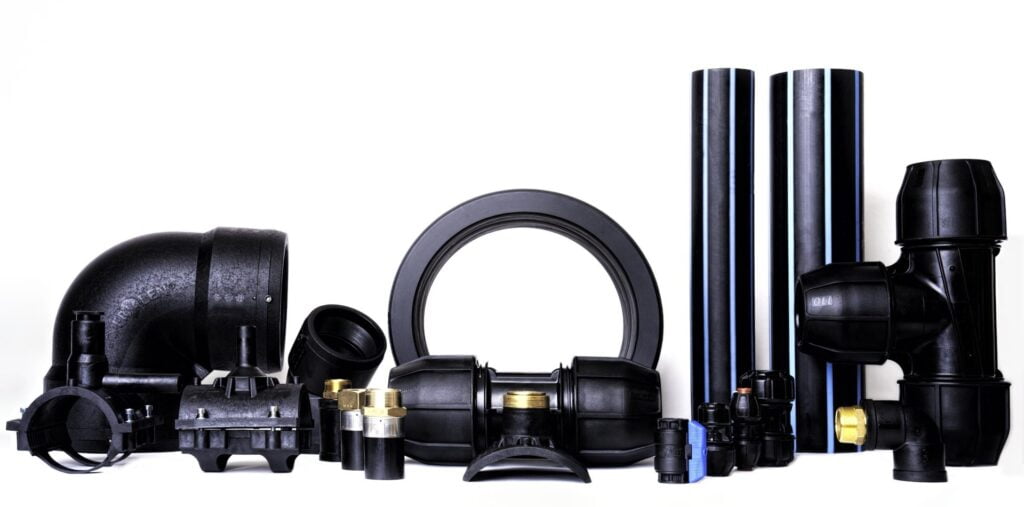
What is HDPE Pipe?
HDPE pipes are made from high-density polyethylene resin, a versatile material known for its strength, flexibility, and chemical resistance. These pipes are commonly used in various industries for the transportation of water, gas, and other fluids due to their superior performance and longevity.
Benefits of HDPE Pipes
- Durability: HDPE pipes are known for their high durability and resistance to corrosion, making them suitable for both above-ground and underground applications.
- Flexibility: HDPE pipes are flexible and can be easily bent to accommodate changes in terrain, reducing the need for additional fittings and joints.
- Chemical Resistance: HDPE pipes are resistant to chemicals, making them ideal for use in industrial applications where exposure to harsh chemicals is common.
- Leak-free Joints: HDPE pipes can be joined using heat fusion techniques, creating seamless, leak-free joints that prevent water loss and ensure long-term reliability.
- Environmentally Friendly: HDPE pipes are recyclable and environmentally friendly, reducing the impact on the environment and promoting sustainability.
Applications of HDPE Pipes
- Water Supply: HDPE pipes are commonly used for water distribution systems in residential, commercial, and municipal settings due to their high flow capacity and resistance to corrosion.
- Gas Distribution: HDPE pipes are widely used for the distribution of natural gas and other gases due to their ability to withstand high-pressure environments.
- Mining and Industrial Applications: HDPE pipes are used in mining and industrial settings for the transportation of abrasive slurries, chemicals, and wastewater.
- Irrigation: HDPE pipes are ideal for irrigation systems due to their flexibility, resistance to root penetration, and long service life.
- Landfill and Drainage Systems: HDPE pipes are used in landfill and drainage systems for their resistance to chemicals and ability to handle high-impact loads.
Installation of HDPE Pipes
- Preparation: Ensure the pipe ends are cleaned and beveled to create a smooth surface for proper fusion.
- Heat Fusion: Use heat fusion techniques such as butt fusion, socket fusion, or electrofusion to join HDPE pipes, forming a strong, leak-free connection.
- Trenching and Bedding: Properly trench and bed the HDPE pipes to accommodate soil conditions and prevent damage to the pipe during installation.
- Pressure Testing: After installation, conduct pressure testing to ensure the integrity of the HDPE pipe system and identify any leaks or defects.
- Maintenance: Regular maintenance and inspection of HDPE pipes are essential to prolong their service life and prevent potential issues.
In conclusion, HDPE pipes offer numerous benefits, versatile applications, and efficient installation methods that make them a preferred choice for various piping systems. Whether you are looking for a reliable water supply solution, gas distribution system, or industrial piping network, HDPE pipes can meet your requirements with unmatched performance and longevity. Welcome to consult , dcpipe-original manufacturer of industrial pipes