In recent years, there has been a growing emphasis on the use of advanced materials in various industries, particularly within the construction and engineering sectors. One such material that has garnered significant attention is Glass Reinforced Plastic (GRP), a composite material which has revolutionized traditional practices through its versatility and robustness. This blog post aims to provide a thorough exploration of GRP pipes, covering their properties, applications, production processes, and the benefits they offer in various settings.
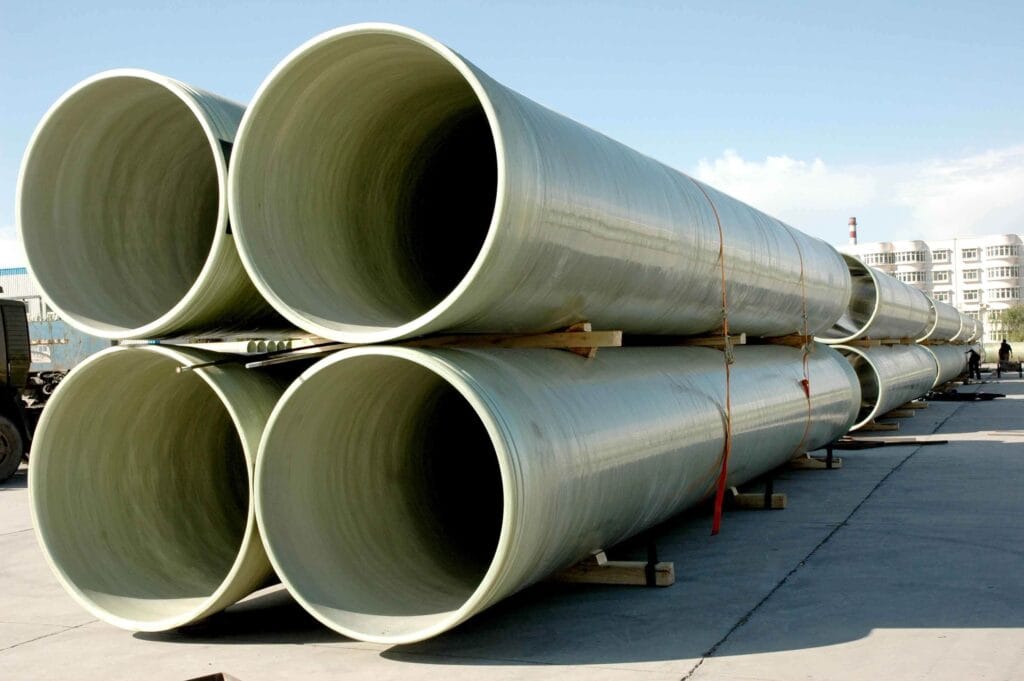
What are GRP Pipes?
Glass Reinforced Plastic pipes, commonly referred to as GRP pipes, are a type of composite pipe made from thermosetting resins reinforced with glass fibers. The combination of glass fibers and resin results in a material that exhibits high strength, low weight, and excellent resistance to corrosion, making GRP pipes a favorable alternative to conventional pipe materials such as metal and concrete.
Composition
GRP pipes are composed of two primary components:
- Matrix Material: The matrix is typically a thermosetting resin, such as polyester, vinyl ester, or epoxy. This resin provides the overall shape and acts as a binder for the glass fibers.
- Reinforcement: The reinforcement consists of glass fibers that enhance the mechanical properties of the resin, providing strength and stiffness.
The ratio of resin to reinforcement, the type of glass fibers used, and the manufacturing process play crucial roles in determining the performance characteristics of the final product.
Properties of GRP Pipes
GRP pipes possess several unique properties that set them apart from traditional pipe materials:
1. Corrosion Resistance
GRP pipes are inherently resistant to a wide range of chemicals and environmental conditions. This characteristic makes them ideal for applications in industries where exposure to harsh chemicals is common, such as sewage transport, chemical processing, and water treatment.
2. Lightweight
One of the most significant advantages of GRP pipes is their low weight compared to steel or concrete pipes. This feature simplifies handling, transportation, and installation, reduces labor costs, and minimizes the need for heavy lifting equipment.
3. High Strength-to-Weight Ratio
GRP pipes exhibit an impressive strength-to-weight ratio. This means they can withstand significant internal and external pressure while remaining lightweight. This property is crucial for applications where structural integrity is paramount.
4. Thermal Insulation
The thermal insulation properties of GRP pipes help in minimizing heat loss in applications where temperature control is vital. For instance, in the transport of hot water, GRP pipes can maintain higher temperatures longer than their metal counterparts.
5. Longevity
With appropriate maintenance, GRP pipes can have a life expectancy of more than 50 years. This durability translates into reduced lifetime costs and fewer replacements.
Applications of GRP Pipes
The versatility of GRP pipes allows for their use across a wide range of sectors. Here are some key applications:
1. Water Supply and Distribution
GRP pipes are increasingly used in municipal water supply systems due to their corrosion resistance and leakage prevention. They are suitable for both potable water and raw water transport.
2. Wastewater Management
In sewage and wastewater treatment plants, GRP pipes offer excellent resistance to corrosive substances found in sewage. They are used for both gravity and pressured sewer systems.
3. Industrial Applications
Many industries utilize GRP pipes for transporting corrosive chemicals. The oil and gas sector, in particular, favors GRP pipes for transporting hydrocarbons and other corrosive fluids.
4. Irrigation Systems
Due to their lightweight nature and resistance to soil chemicals, GRP pipes are extensively used in agricultural irrigation systems, contributing to efficient water management practices.
5. Marine and Offshore Applications
The marine industry leverages GRP pipes for various applications, including drainage, ballast, and cooling water systems, thanks to their resistance to seawater corrosion.
Manufacturing Processes
The production of GRP pipes can be achieved through several methods, including:
1. Filament Winding
This is one of the most common techniques where glass fibers are wound around a mandrel in a specific pattern and coated in resin. The process allows for the control of the fiber orientation, which can be tailored to meet specific strength requirements.
2. Centrifugal Casting
In this method, resin and glass fibers are fed into a rotating mold. The centrifugal force ensures that the materials distribute evenly, resulting in a uniform wall thickness and density.
3. Pultrusion
Pultrusion involves continuously pulling glass fiber reinforced resin through a heated die to create pipes with a constant cross-section. This method is particularly effective for producing long, straight pipes.
Advantages of GRP Pipes
The advantages of GRP pipes extend beyond their basic properties and applications. They include:
1. Economic Benefits
While the initial cost of GRP pipes may be higher than traditional materials, their longevity, reduced maintenance needs, and lower installation costs often result in lower overall lifecycle costs.
2. Environmental Impact
GRP pipes are often perceived as more environmentally friendly than their metal counterparts. Their longer lifespan and resistance to corrosion mean less frequent replacements and lower resource consumption over time.
3. Customization
GRP pipes can be manufactured to meet specific project requirements, including diameter, thickness, lengths, and fittings. Customizable solutions allow for flexibility in design and application.
4. Minimal Disruption
The lightweight nature of GRP pipes leads to less ground disturbance during installation. This is particularly beneficial in urban areas where minimizing disruption is crucial.
Conclusion
In summary, GRP pipes represent an innovative and practical solution for various piping needs across numerous industries. Their unique combination of properties, including corrosion resistance, lightweight design, and high strength, positions them as an optimal choice in modern engineering applications. As industries continue to seek materials that aid in efficiency, sustainability, and cost-effectiveness, it is highly likely that the adoption of GRP pipes will continue to grow, cementing their place in the future of infrastructure development.
Whether for water supply, irrigation, or industrial use, GRP pipes provide a comprehensive solution that is well-suited to meet the demands of today’s engineering challenges. Understanding their properties, advantages, and potential applications is crucial for engineers, project managers, and decision-makers as they strive to implement the best practices in their respective fields. dcpipe-piping system expert