PE (polyethylene) materials are widely used due to their excellent properties. However, there are significant differences in the usage and characteristics between PE water supply pipes and PE gas pipes.
Firstly, in terms of usage, PE water supply pipes are mainly used in urban water supply systems to provide clean drinking water for residents and industries. PE gas pipes are specifically used to transport natural gas and other gases, providing energy for residents and industrial production. These two types of pipelines play a crucial role in their respective fields. Based on years of practical experience, Dingchang Xinlong has summarized the following experiences for your reference. If you have any technical exchanges, please feel free to call 400-0533-612.
Usage Differences
● PE Water Supply Pipes:
○ Primarily used in urban water supply systems.
○ Provide clean drinking water for residents and industries.
● PE Gas Pipes:
○ Specifically used to transport natural gas and other gases
○ Provide energy for residents and industrial production.
○ Safety and stability of gas transmission are paramount.
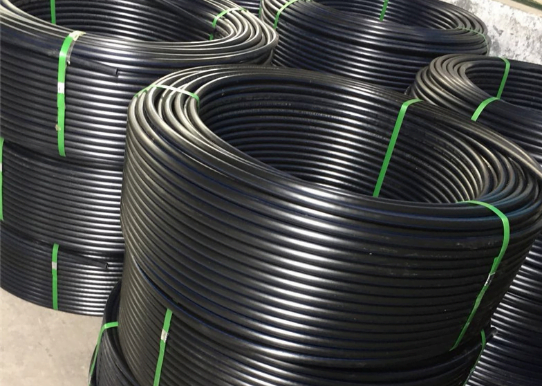
Material Properties
PE water supply pipes are made of PE80 or PE100 grade high-density polyethylene, using primary color colorants added to a certain proportion of colorants according to the formula to increase oxidation resistance, and then heated to produce extrusion. PE pipes pay more attention to corrosion resistance and hygiene performance, and cannot pollute water quality. There should be no odor in the water, and there should be testing requirements for hygiene performance indicators of the pipes to ensure the safety of water quality and the long-term use of the pipes.
● PE Water Supply Pipes:
○ Made of PE80 or PE100 grade high-density polyethylene.
○ Use primary color colorants to increase oxidation resistance.
○ Focus on corrosion resistance and hygiene performance.
○ Must not pollute water quality or produce any odor.
○ Must meet hygiene performance indicators to ensure water quality safety and long-term use.
● PE Gas Pipes:
○ Emphasize pressure resistance and leakproofness.
○ Use uniform carbon black distribution and better anti-aging materials.
○ Design life of 50 years with a service life of no less than 30 years.
○ Implement a lifelong responsibility system.
○ Higher requirements due to the potential danger of gas leaks.
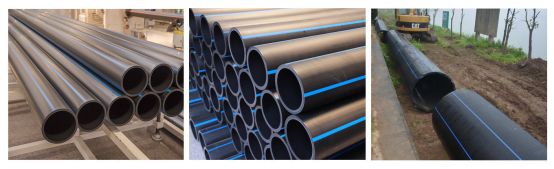
Installation and Use Differences
In addition, Dingchang Xinlong reminds that there are differences in the installation and use of PE water supply pipes and PE gas pipes. Due to the water pressure and impact force that the water supply pipe needs to withstand, it is generally necessary to use hot melt connection or electric melt connection during installation to ensure the sealing and reliability of the pipeline.
There is no strict requirement for the diameter, and it can be adjusted according to the construction site conditions. Gas pipes, on the other hand, require strict testing and pressure testing before installation.
Pipes with a diameter below DN63 must be welded using electric fusion welding, while pipes between DN63-DN110 are recommended to be welded using electric fusion welding as a priority. For gas pipes with a diameter above DN110, there are no special requirements for welding methods to ensure that there will be no safety accidents such as leaks during use.
● PE Water Supply Pipes:
○ Must withstand water pressure and impact forces.
○ Use hot melt or electric melt connections during installation to ensure sealing and reliability.
○ No strict requirements for diameter, adjustable based on construction site conditions.
● PE Gas Pipes:
○ Require strict testing and pressure testing before installation.
○ Pipes with a diameter below DN63 must be welded using electric fusion welding.
○ Pipes with a diameter between DN63 and DN110 are recommended to be welded using electric fusion welding as a priority.
○ For gas pipes with a diameter above DN110, no special welding method requirements.
○ Ensure no safety accidents such as leaks during use.
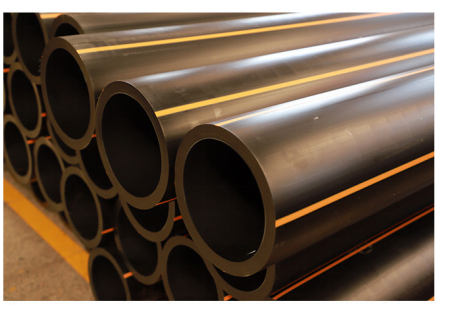
Summary and Contact
Dingchang Xinlong’s Expertise
Years of practical experience in the field.
Summarized insights and best practices for reference.
For technical exchanges, contact: 400-0533-612.